Project Cargo Transport
Projests : Thermal Power Project
Chile
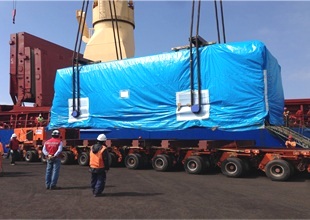
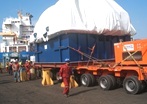
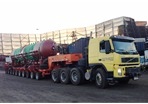
The Republic of Chile was in need of power generation facilities to address a sudden rise in electricity demand and the need for power infrastructure resulting from strong economic growth sparked by a rise in the international price of copper, a resource of which the country has vast supplies. We were selected by one of our valuable clients tapped for a thermal power plant construction project to provide overland transport services for the materials and equipment related to the construction project. To ensure our ability to provide safe and reliable logistics services that would meet the needs of the customer, we established a local subsidiary in the target country and provided transport services.
This large-scale project involved heavy-lift cargo weighing more than 200 tons per unit as well as oversized cargo more than 20 meters in length. We dispatched supervisors to Chile in order to work in close collaboration with the local subsidiary and ensured the provision of safe and secure transport services.
Southern Luzon, Philippines
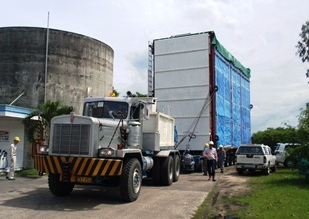
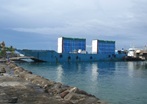
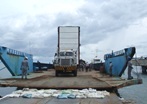
Below, we introduce a project that took place July 2013 in Quezon City, Philippines, where we provided intermodal transport services (ocean and overland transport) for a condenser to be used in a coal-fired power plant.
This project involved the intermodal transport of a condenser (device that cools and concentrates steam (low-pressure wet steam) inside a turbine or cylinder at a uniform pressure and returns the steam to a low-pressure saturated liquid) from Japan to Quezon City, Philippines for use in an existing coal-fired power plant.
The weight of the condenser main unit was 100 tons with a cargo width of 4.6m and height of 7.5m. This sized equipment required us to load the cargo onto a LCT (Landing Craft Tank) barge at a major port in the Philippines and transport the cargo by sea to the construction site.
As unloading the cargo from the LCT barge using a crane would require the use of a large-scale crane, we identified a site within the construction site where we could conduct unloading via roll-off and used gravel and sand to create a slope required for unloading. We loaded the cargo onto a 10-axle dolly and pulled to unload the cargo from the LCT barge and transport it to the final delivery site.
The height of the condenser on the 10-axle dolly was nearly nine meters. As such, we conducted on-site surveys and several.
Meetings with the customer to plan the removal of lights, gates, and other aerial obstructions. We also planned laying steel plates to cure embedded objects under the road at the construction site and confirmed tidal data necessary for the roll-off procedure, the barge angle and roll-off plan. The customer praised our ability to complete the project without incident or schedule delays.